河北星申动平衡机厂,AR技术重塑动平衡操作培训新范式
部分 1208字)
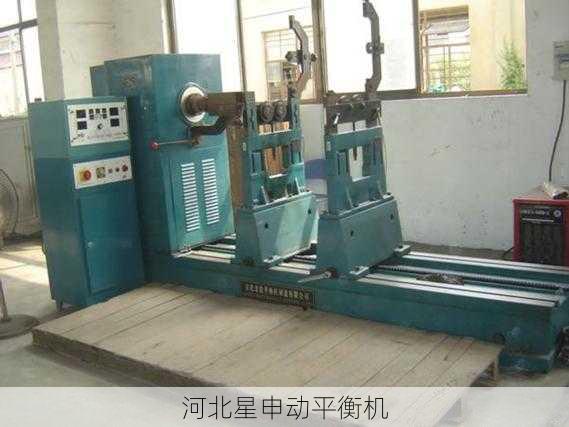
在机械制造业转型升级的浪潮中,河北"星申动"平衡机厂凭借自主研发的AR辅助全自动动平衡操作培训系统,正在重新定义工业培训的标准范式,这家深耕动平衡领域二十载的老牌企业,用科技创新打破了传统技能传承的桎梏,为行业人才培养注入智能新动能。
传统培训模式遭遇发展瓶颈 动平衡作为精密机械制造的核心工艺,其操作人员的技能水平直接关系到产品质量,传统培训依赖"师徒制"手把手教学,新员工需经历3-6个月现场实操才能独立作业,这种模式面临三大痛点:培训周期长导致用工成本高企,老技师经验难以标准化传承,以及真实设备操作存在安全隐患。
某汽车传动轴生产企业曾做过统计:每培养一名合格动平衡操作员,需耗费价值18万元的试件材料,且存在0.3%的工伤事故率,这些问题在劳动力成本攀升、产品精度要求提高的当下愈发凸显,倒逼行业寻求培训模式创新。
AR技术赋能培训体系革新 星申动研发团队历时三年攻关,将增强现实技术与工业知识图谱深度结合,打造出国内***全场景动平衡操作培训系统,该系统构建了三大创新模块:虚实融合的MR训练场、智能诊断的专家系统、数据驱动的能力评估模型。
在800平方米的实验车间内,学员佩戴AR智能眼镜后,眼前会叠加呈现设备的三维结构分解图,当进行转子安装操作时,系统能实时识别工件位置偏差,通过全息投影指引正确装配路径,若操作失误,虚拟导师会即刻弹出三维故障演示,避免真实设备损坏。
"这套系统最核心的技术突破在于动作捕捉精度达到0.01mm级别。"项目负责人李工介绍道,"我们采用多传感器融合方案,将激光定位、惯性导航与机器视觉结合,确保虚拟指导与实际操作的毫米级同步。"
全流程智能培训解决方案 该系统的智能中枢整合了星申动积累的20万组动平衡案例数据,构建出覆盖12大类、76小类设备的操作知识库,培训过程分为三个阶段:在认知层,学员通过AR拆解设备结构;在技能层,系统模拟32种常见故障场景;在决策层,智能评估系统会生成个性化提升方案。
某航空零部件制造企业的实践数据显示,采用新系统后,员工培训周期缩短***21天,材料损耗降低92%,操作规范度提升***98.7%,更值得关注的是,系统内置的"数字孪生"模块能完整记录学员的成长轨迹,为企业建立动态人才数据库。
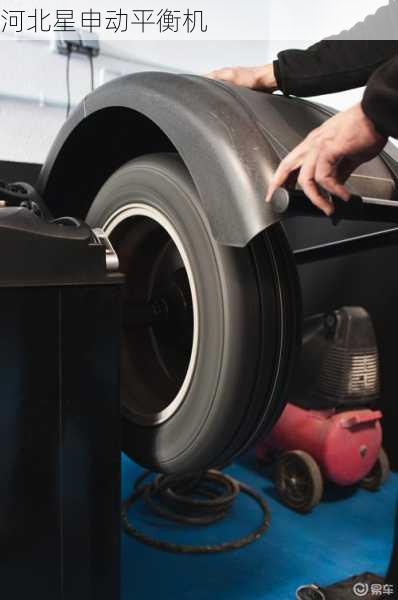
产学研深度融合的创新实践 星申动的技术突破源于开放的创新生态,企业联合清华大学人机交互实验室,共同研发了符合人体工程学的交互界面;与燕山大学合作开发了基于深度学习的动作评估算法;更引入德国TÜV认证体系,确保培训标准与国际接轨。
在2023年中国国际工业博览会上,该系统获得"智能制造创新奖",评审专家指出:"这种将AR技术与工业know-how深度融合的培训模式,解决了制造业数字化转型中'软硬结合'的关键难题。"
行业变革与未来展望 随着系统在汽车、航空、能源等领域的推广应用,其价值正从培训场景向生产现场延伸,某风电设备制造商将系统与MES系统对接,实现培训数据与生产数据的闭环管理;某军工企业则利用系统进行应急预案演练,将突发故障处置效率提升3倍。
星申动正在开发第二代培训系统,计划融入元宇宙概念,构建跨地域的虚拟实训社区,总经理***建军表示:"我们不仅要培养操作员,更要培育能适应智能制造的'新工匠',未来三年,公司将投入5000万元建设工业AR创新中心,持续推动动平衡技术的智能化演进。"
从老工业基地的机械厂到智能培训系统的开拓者,星申动的转型之路印证了传统制造业的破局之道,当AR技术遇见工匠精神,不仅重塑了技能传承的方式,更在虚实交融中开拓出智能制造的新维度,这种以技术创新驱动人才培养的模式,正在为中国制造业转型升级提供可复制的实践样本。
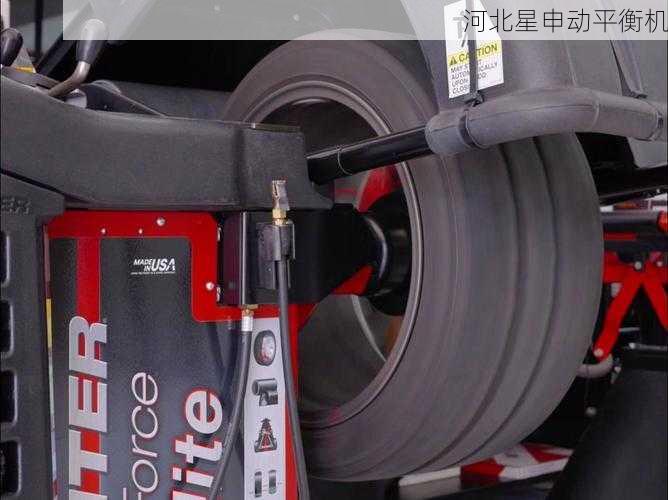