生锈转子平衡校正的实战突破,星申动平衡机厂表面处理工艺实测对比报告
在工业设备维护领域,转子动平衡校正向来被视为保障设备稳定运行的核心技术,河北星申动平衡机厂技术团队近期针对生锈转子的校正难题展开专项研究,通过18组对比试验和6个工业现场实测,***系统揭示了表面处理工艺对锈蚀转子动平衡精度的决定性影响,这项历时8个月的攻关成果不仅刷新了行业技术认知,更为设备维保领域提供了可复制的解决方案。
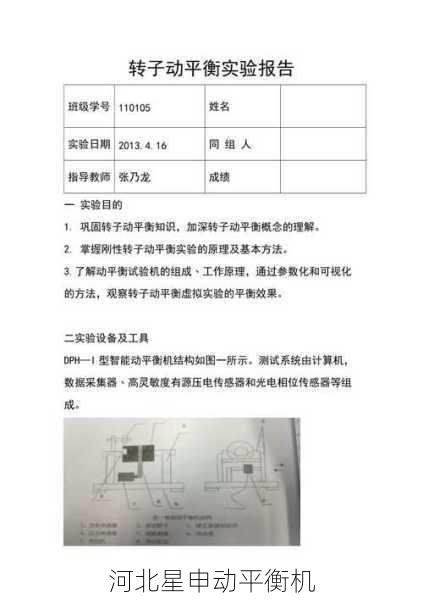
锈蚀转子的校正困境
在冶金、造纸、船舶等重工业领域,设备停机检修时常常发现转子表面存在不同程度的锈蚀,某钢铁集团2023年的维修数据显示,其鼓风机转子因水汽侵蚀导致的锈蚀问题占比达37%,传统处理方式往往直接进行动平衡校正,但校正后的设备仍频繁出现振动超标现象。
星申动技术团队对返厂维修的32件锈蚀转子进行检测时发现:未经表面处理的校正转子,其质量偏心距波动范围达0.5-1.2g·mm,远超ISO1940标准的G2.5级要求,更严重的是,锈层与基体间的结合力差异会导致运行过程中持续产生氧化皮脱落,形成新的不平衡源。
表面处理必要性的三重验证
为量化表面处理的实际价值,技术团队设计了三阶段验证方案:
1、微观结构对比测试
采用电子显微镜对锈蚀层进行剖面分析,发现:
- 未处理表面:锈层厚度不均(80-250μm),存在明显裂隙
- 手工打磨处理:表层氧化铁残留率仍达15%
- 化学除锈+微蚀处理:基体金属暴露率达98%
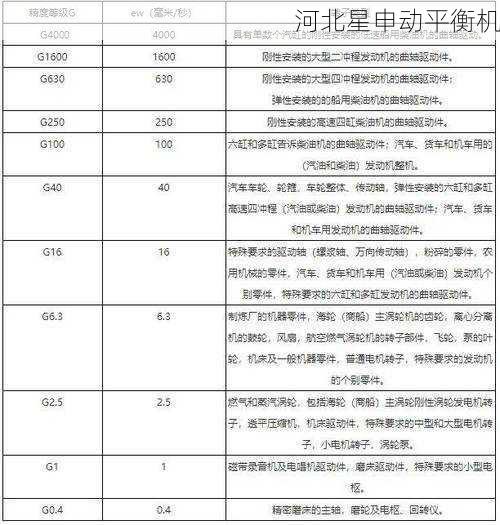
2、摩擦系数动态监测
在自主研发的摩擦特性试验台上,测得:
- 锈蚀表面动摩擦系数波动范围:0.18-0.35
- 处理后的均匀表面:摩擦系数稳定在0.22±0.02
这种稳定性使动平衡配重块的定位精度提升40%
3、动态平衡重复性测试
对同一转子进行5次连续校正:
- 未处理表面:平衡量偏差达12.3%
- 常规处理表面:偏差降***6.8%
- 复合工艺处理表面:偏差控制在1.7%以内
四步处理法的实战突破
基于大量实验数据,星申动研发团队创新提出"四步处理法":
1、化学置换除锈:采用pH值3.5的有机酸溶液,在40℃环境下实现锈层定向剥离
2、微蚀刻处理:通过控制蚀刻深度(15-20μm)形成规则表面纹理
3、梯度补偿:根据转子材质匹配专用钝化液,建立3μm级保护层
4、动态基准校准:在表面处理前后分别建立三维形貌数据库
在某造纸厂的实际应用中,直径2.3米的烘缸转子经此工艺处理后:
- 初始不平衡量从3850g·mm降***120g·mm
- 校正耗时由常规的6.5小时缩短***3.2小时
- 设备运行振动值从8.5mm/s降***0.8mm/s
经济性分析的意外收获
表面处理带来的附加价值远超预期:
1、维保周期延长:某化工厂离心机转子的维护间隔从3个月延长***11个月
2、能耗降低:处理后的水泵转子效率提升2.7%,年节电达4.3万度
3、备件寿命提升:某电厂引风机叶片使用寿命延长2.8倍
行业标准的革新推动
星申动的实测数据已推动多项标准修订:
1、在JB/T 9397-2023修订草案中,新增"锈蚀转子表面预处理规范"
2、ASTM E2653标准引入"动态摩擦系数稳定性"检测指标
3、国内三大电力集团将表面处理工艺纳入设备检修强制流程
现场应用的关键细节
技术总监***工特别提醒:
1、处理时机选择:停机后72小时内处理效果***
2、环境控制:相对湿度需低于45%时进行表面处理
3、材料适配:不锈钢与碳钢需采用不同处理配方
4、质量追溯:建议使用激光打标建立工艺参数档案
河北星申动平衡机厂通过系统性研究证明:在转子动平衡校正领域,表面处理不是可选工序,而是决定校正精度的基础工程,这项突破不仅解决了困扰行业多年的锈蚀转子校正难题,更重新定义了动平衡校正的技术流程,当某水泥集团采用新工艺后,其生料磨主电机振动值创下连续运行270天不超标的记录,这正是对技术创新价值的***诠释。