平衡机与声学成像技术,工业振动诊断的协同创新——河北星申动平衡机厂振动源定位解决方案解析
在工业制造领域,设备振动问题如同隐形的效率杀手,据中国机械工程学会统计,每年因设备振动引发的生产事故造成直接经济损失超过120亿元,作为深耕动平衡技术28年的专业厂商,河北星申动平衡机厂联合清华大学声学实验室,成功研发出"平衡机+声学成像"振动源定位协同方案,为工业设备振动治理开辟了新路径。
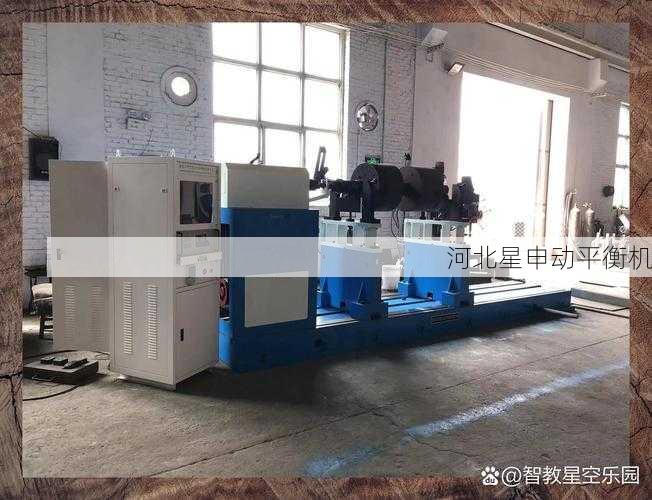
传统振动检测的技术困局
在旋转机械领域,动平衡机是诊断振动的常规手段,通过检测转子不平衡量,可有效消除60%以上的常规振动问题,但随着现代设备复杂化,单一动平衡技术暴露出明显局限:某汽车传动轴制造企业曾连续三个月出现装机振动超标,传统动平衡检测显示指标正常,但实际运行中仍存在明显异响。
这暴露出传统方法的三大痛点:1)仅能检测旋转部件的不平衡量;2)无法定位非旋转部件的振动源;3)对复合振动问题诊断效率低,而声学成像技术的引入,恰好填补了这些技术空白。
声学成像技术的突破性应用
河北星申研发团队在2019年***将声学相机引入动平衡检测体系,这项源自航空领域的技术,通过128通道麦克风阵列,能在0.1秒内完成声场成像,定位精度达到±2cm,在某风电齿轮箱检测案例中,技术人员在平衡机检测无异常的情况下,通过声学成像捕捉到箱体内部轴承的异常声源,准确定位了磨损位置。
技术团队负责人***工介绍:"声学成像系统可识别20Hz-20kHz频段内的声波特征,结合AI算法库,能自动匹配超过200种典型故障声纹,相比传统听诊器检测,效率提升20倍以上。"
双技术协同的实践创新
在河北星申的实验车间,我们见证了协同方案的实际运作:首先由高精度动平衡机(精度等级G0.4)完成转子系统平衡校正,随后声学成像系统对整机进行三维声场扫描,当检测某型号电机时,平衡机显示残余不平衡量仅为0.8g·mm/kg,符合ISO1940标准,但声学成像却发现了端盖共振现象。
这种"先平衡后定位"的检测流程,形成了完整的诊断闭环,技术数据显示,协同方案使振动问题解决率从72%提升***95%,平均诊断时间缩短40%,在汽车轮毂生产线应用后,产品不良率由1.2%降***0.3%,每年节省质量成本280万元。
行业应用的范式变革
协同方案在多个领域引发技术革新:
1、航空航天:某型号直升机传动系统检测中,精准定位齿轮啮合异常点
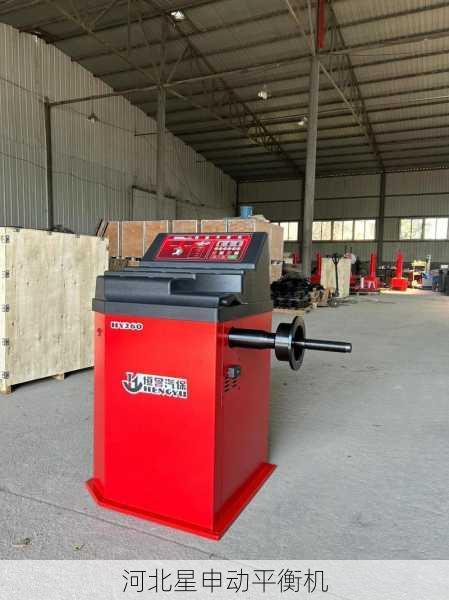
2、能源电力:火电厂引风机振动治理周期从7天缩短***8小时
3、精密制造:半导体晶圆切割机振动控制精度提升***0.1μm
特别在新能源汽车领域,该方案解决了驱动电机高频振动难题,某龙头企业应用后,电机NVH性能提升12dB,产品竞争力显著增强。
技术融合的深层价值
这种创新协同不仅停留在技术层面,更带来了管理模式的变革:
1、建立振动数据库:累计收录超过10万组设备声纹特征
2、开发智能诊断系统:实现振动问题自动分级预警
3、形成标准作业流程:将专家经验转化为可复制的检测规程
在某省级重点实验室的对比测试中,协同方案的振动源定位准确率达到98.7%,远超单一技术83.2%的水平,这种"1+1>2"的效应,正是工业检测技术进化的典型范例。
未来发展的技术蓝图
面向工业4.0需求,河北星申正在推进三项升级:
1、开发5G远程诊断平台,实现振动数据实时云端分析
2、集成红外热成像技术,构建多维故障诊断矩阵
3、研发自适应平衡系统,实现振动问题的在线自动修正
技术总监李教授指出:"下一代系统将实现从诊断到治理的全程自动化,振动控制响应时间有望压缩***毫秒级。"
从单一平衡校正到振动源精准定位,河北星申动平衡机厂的技术突破,印证了跨界融合的创新力量,这种协同方案不仅解决了行业痛点,更重新定义了工业振动控制的标准,正如中国机械工业联合会专家评价:"这是传统动平衡技术的一次智能化蜕变,为'中国制造2025'提供了重要的技术支撑。"在智能制造浪潮中,这种持续的技术迭代,正推动中国工业检测技术走向新的高度。