动平衡技术解析
动平衡技术作为机械工程领域的重要课题,其发展历程和应用价值值得深入探讨。本文将从基本原理、技术实现、应用场景和发展趋势四个维度进行详细解析。
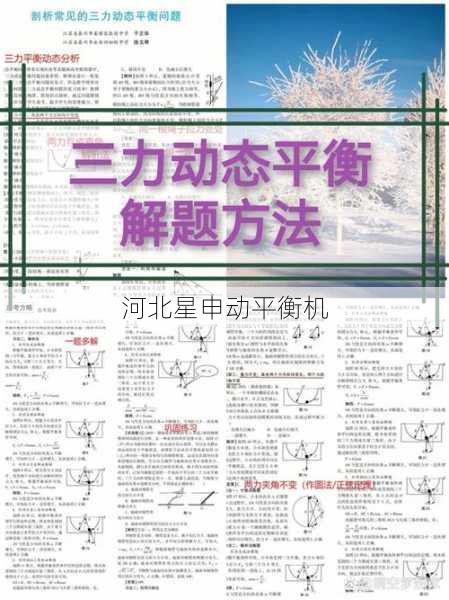
一、动平衡的基本原理
动平衡技术的核心在于消除旋转部件的不平衡量😊。根据力学原理,当转子旋转时,任何微小的质量偏心都会产生离心力,其大小与不平衡量、转速平方成正比。这种不平衡力会导致设备振动加剧、轴承磨损加快,严重时甚***引发安全事故。
动平衡的实现需要遵循两个基本条件:1)力的平衡;2)力矩的平衡。工程师们通过***计算和调整,在转子的特定位置添加或去除材料,使惯性主轴与旋转轴线重合,从而达到平衡状态👍。
二、技术实现方法
现代动平衡技术主要分为三类实现方式:
1. 现场动平衡 :直接在设备运行状态下进行平衡校正,适用于大型机组。这种方法不需要拆卸设备,通过振动传感器采集数据,利用影响系数法计算配重方案。其优势是能反映实际工况,但技术要求较高😉。
2. 平衡机校正 :使用专用动平衡机进行离线平衡。典型的硬支承平衡机采用压电传感器测量不平衡力,软支承平衡机则通过测量振动位移。平衡精度可达0.1g·mm/kg,适用于批量生产的零部件。
3. 自动平衡系统 :集成传感器、控制器和执行机构的智能系统。如采用液体平衡环的洗衣机,通过实时检测和自动调节,实现运行过程中的动态平衡。这类系统代表了未来发展方向🌟。
三、典型应用场景
动平衡技术已渗透到各个工业领域:
汽车工业 :轮胎动平衡是保证行驶平顺性的关键。现代轮胎平衡机采用激光测量,配合自学习算法,能在30秒内完成平衡校正。发动机曲轴的平衡要求更为严格,残余不平衡量通常控制在1g·cm以内🚗。
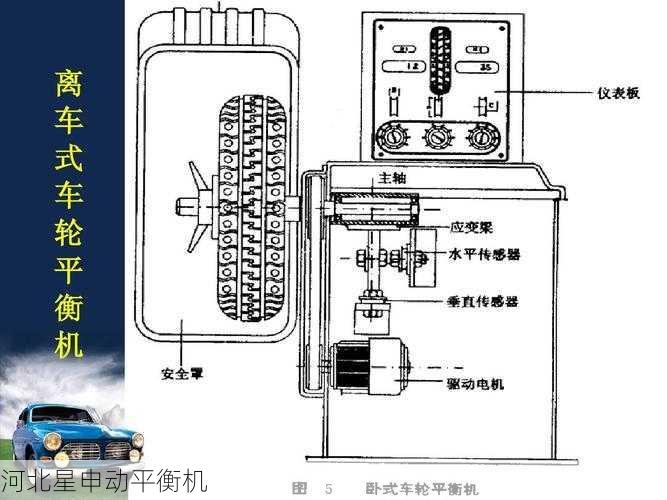
能源装备 :大型汽轮发电机组的转子重量可达数百吨,平衡精度要求极高。采用多平面平衡技术,配合有限元分析,将振动值控制在25μm以下。风电叶片的现场平衡更是关系到整机寿命💨。
精密制造 :高速主轴、陀螺仪等精密部件的平衡等级要求达到G0.4级。需要在高洁净环境中,使用空气轴承平衡机进行微克级的质量调整。半导体制造设备中的真空腔体转子,其平衡精度直接影响晶圆加工质量🔬。
四、技术发展趋势
随着工业4.0的推进,动平衡技术正在经历智能化变革:
1. 数字孪生应用 :通过建立转子系统的数字孪生模型,可以预测不同转速下的振动特性,实现虚拟平衡调试。某航空发动机企业采用该方法后,试车次数减少40%✈️。
2. 自适应平衡算法 :基于深度学习的平衡算法能够自动识别不平衡特征,如某企业开发的CNN网络模型,对复杂转子的不平衡定位准确率达95%以上。
3. 新型平衡装置 :磁流变平衡装置通过调节磁场强度改变配重分布;微机电系统(MEMS)平衡器可实现纳米级调节,这些创新技术正在拓展动平衡的应用边界⚡。
4. 云平台监测 :工业物联网(IIoT)技术使远程动平衡监测成为可能。某电厂通过云平台实时监控20台机组的振动数据,实现预测性维护,年维修成本降低28%☁️。
五、技术挑战与对策
当前动平衡技术仍面临若干挑战:
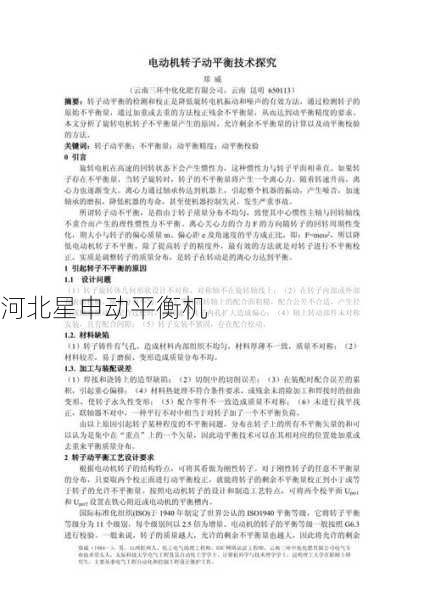
对于柔性转子的平衡,需要考虑轴系变形的影响。建议采用模态平衡法,在工作转速附近选择多个平衡面。超临界转子的平衡则需要考虑陀螺效应,目前正在发展的全息动平衡技术有望解决这一难题💡。
微型化设备的平衡需求日益突出。建议研发基于视觉测量的微转子平衡系统,结合机器视觉和精密运动控制,实现亚微米级平衡。同时,新材料应用带来的平衡问题也需要关注,如碳纤维复合材料的各向异性特性😊。
动平衡技术正在向智能化、精准化、系统化方向发展。未来随着5G、AI等新技术的融合,必将推动动平衡技术进入新的发展阶段✨。