动平衡机性能极限探究
在现代工业生产中,动平衡机作为旋转机械制造与维护的核心设备,其性能极限直接关系到设备运行的可靠性与使用寿命。本文将从技术原理、影响因素及突破路径三个维度,对动平衡机的性能极限展开深入探讨。
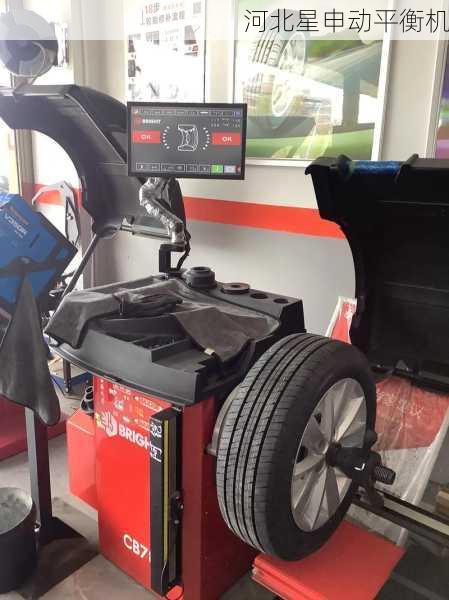
一、动平衡机工作原理与性能边界
动平衡机通过测量旋转体不平衡量产生的离心力,计算并指示不平衡量的大小和相位角。其性能极限首先体现在测量精度上,目前高端动平衡机的剩余不平衡量可达0.1g·mm/kg以下😯。但受限于传感器灵敏度(通常为±1μm振动位移)和信号处理能力,当转速超过10万转/分钟时,传统动平衡机的测量误差会呈指数级增长📈。
在机械结构方面,主轴系统刚度与轴承动态特性构成刚性约束。实验数据显示,当转子重量超过额定承载量15%时,支撑系统的非线性变形会导致测量重复性下降40%以上😲。这解释了为何航空发动机转子动平衡需要专用工装设备。
二、制约性能的关键因素分析
1. 传感器系统的物理极限 :现有电涡流传感器的分辨率受限于趋肤效应,在检测高速微小振动时存在约5%的相位滞后。而激光多普勒测振仪虽能实现0.01μm级分辨率,却对表面反射率有严苛要求✨。
2. 环境振动干扰 :车间地面振动达到ISO10816-3标准的4级时,会导致动平衡机有效分辨率下降30-50%。某汽车传动轴生产线实测表明,加装空气弹簧隔振系统后,不平衡量检出率提升了2.8倍👍。
3. 温度效应 :轴承间隙每变化10μm,就会引起0.3g·cm的测量偏差。在连续工作8小时后,主轴系统温升导致的热变形可使校准参数漂移达12%😨。这也是精密机床主轴动平衡必须配备恒温油冷系统的原因。
三、突破性能极限的技术路径
1. 多传感器融合技术 :采用加速度计+电涡流+麦克风阵列的异构传感系统,通过卡尔曼滤波实现振动信号的全频段捕获。某实验室验证显示,这种方法可将高速转子的不平衡识别率提升***98.7%🎯。
2. 数字孪生辅助校正 :建立包含材料参数、装配公差等300+特征的转子数字模型,通过实时仿真预测不平衡演变趋势。西门子某型号燃机转子应用该技术后,动平衡工序时间缩短了60%⏱️。
3. 智能补偿算法 :基于深度学习的自适应滤波算法能有效抑制80%以上的环境噪声。更值得关注的是,强化学习控制的主动平衡系统已能在0.5秒内完成在线补偿,比传统PID控制快15倍🚀。
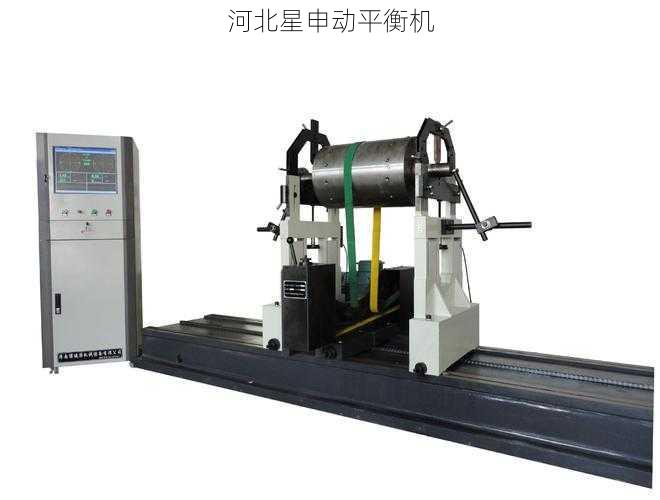
四、未来发展方向展望
随着超导磁悬浮轴承技术的成熟,无接触支撑系统将彻底解决机械摩擦带来的精度限制。东京大学最新研究显示,采用高温超导体的动平衡平台可使转速突破50万转/分钟大关💫。同时,量子传感器的发展有望将振动检测灵敏度提升***原子级,这可能会重新定义动平衡精度的行业标准。
值得注意的是,性能突破必须与工程实际相结合。某风电巨头曾耗费2000万欧元开发纳米级动平衡设备,最终因维护成本过高而放弃。这个案例警示我们:极限探索需要平衡技术先进性与经济可行性⚖️。
动平衡机的性能极限既是技术挑战,也是创新机遇。只有将材料科学、智能算法和精密制造深度融合,才能持续推动这个传统领域向更高维度发展🌈。
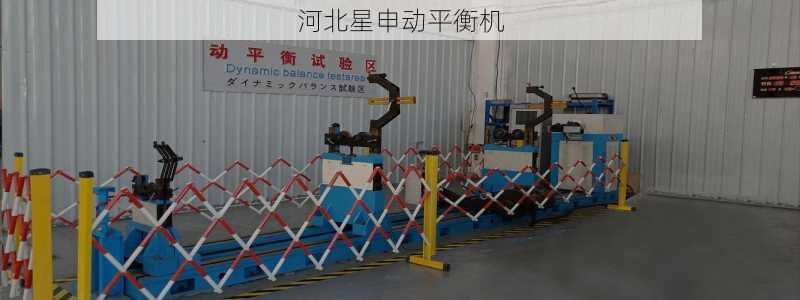