智造革命,河北星申动全自动动平衡技术开启元宇宙工业新纪元
当精密制造遇见数字未来 在河北省石家庄市装备制造产业园内,一座占地3.6万平方米的现代化工厂正掀起一场工业革命,作为中国动平衡装备领域的"隐形***",河北星申动平衡机厂近期推出的"全自动动平衡元宇宙虚拟调试平台",不仅突破了传统制造业的技术天花板,更将工业4.0的想象空间拓展***三维数字世界。
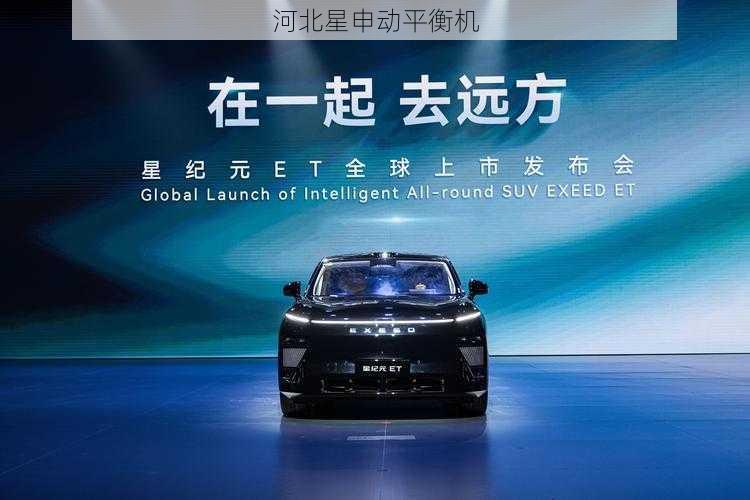
从千分尺到元宇宙的进化之路 在航空发动机转子车间,技术员张立军仍清晰记得十年前的工作场景:操作员需要手持千分尺反复测量工件振动值,每次调整都要经历"停机-拆卸-配重-复测"的循环,一个直径1.2米的叶轮动平衡调试往往耗费8小时,这种传统工艺不仅效率低下,0.05mm的精度波动就可能让价值百万的航空部件报废。
星申动的技术团队用了三年时间攻克这个行业痛点,2020年推出的第三代全自动动平衡系统,将调试时间压缩***45分钟,精度提升***±0.005mm,但真正的突破发生在2023年——当物理世界与数字世界在元宇宙平台实现深度融合,调试效率再次实现指数级跃升。
虚拟调试平台的技术架构 这套革命性系统由三大核心模块构成:
- 数字孪生建模引擎:通过激光扫描与AI算法,在虚拟空间1:1复刻实体设备,某汽车传动轴客户的实际测试显示,平台建立的数字模型与实物偏差不超过3微米。
- 智能平衡算法库:整合了2000余种工业场景数据,能自动识别工件类型并匹配***配重方案,在风电叶片动平衡案例中,系统提出的非对称配重方案使振动值降低27%。
- 元宇宙交互系统:支持VR/AR/MR多模态操作,工程师佩戴智能眼镜即可同时操控3台虚拟设备,沈阳某机床厂使用后,人员培训周期从6个月缩短***18天。
平台最令人惊叹的是其实时响应能力,当物理设备的传感器检测到0.1g·mm的不平衡量时,数字孪生体能在0.3秒内生成3种优化方案,并通过增强现实技术将调整参数投射***操作界面,这种虚实交互的效率,让某无人机马达生产线的产品不良率从1.2%降***0.03%。
重构生产价值链的实践样本 在江苏某精密轴承制造基地,我们见证了元宇宙平台带来的价值重塑,该企业原有6条传统动平衡生产线,每班需要12名技术工人,接入星申动系统后:
- 设备综合效率(OEE)从68%提升***92%
- 单件能耗降低41%
- 异常停机时间减少83%
- 产品交付周期缩短58%
更深远的影响发生在产品研发端,通过虚拟调试平台的仿真测试,某型号高速电机转子的设计迭代次数从17次减少到3次,研发成本节约320万元,这种改变正在重塑制造业的价值链——根据中国机械工业联合会数据,采用类似技术的企业研发效率平均提升40%,售后服务成本降低65%。
工业元宇宙的生态构建 星申动的创新不止于技术突破,更在于构建开放式的工业元宇宙生态,其平台已接入23家上下游企业的数据系统,形成涵盖原材料、加工设备、检测仪器的数字网络,在某新能源汽车联合研发项目中,5家供应商通过虚拟平台同步调试驱动电机系统,将常规需要6个月的协同开发压缩***49天。
这种生态化发展正在催生新的商业模式,2023年第四季度,星申动推出"平衡即服务"(BaaS)订阅模式,中小企业只需支付每工件0.8元的服务费即可使用云端算力,首批试点的85家企业数据显示,设备投资成本平均降低72%,动平衡合格率却提高了19个百分点。

未来工厂的进化方向 站在装备制造业智能化转型的潮头,星申动技术总监***明哲描绘了更宏大的蓝图:"我们正在开发具备自学习能力的第四代系统,当虚拟调试平台积累足够多的工业数据,它不仅能优化当前工序,还能反向指导产品设计、工艺规划和供应链管理。"
这个愿景已初见端倪,在最近的***重点研发计划中,星申动牵头建设的"智能平衡工业互联网平台"成功入选,该平台将整合5G、区块链和量子计算等前沿技术,目标是在2025年实现***设备接入能力,构建覆盖全产业链的动平衡数字生态。
在虚实交融中定义新工业文明 从千分尺的机械时代到元宇宙的数字纪元,河北星申动用十五年时间完成了一场静默而深刻的变革,当问及研发初心时,董事长李卫国给出质朴的回答:"我们不过是想让中国制造少走些弯路。"这句朴实的话语背后,是一个民族企业在智能制造浪潮中的担当与远见。
在这个万物互联的时代,全自动动平衡技术与元宇宙的碰撞,正在书写工业文明的新篇章,它不仅是技术工具的升级,更是生产关系的重构,是制造企业从"物理实体"向"数字生命体"进化的关键一跃,当更多像星申动这样的企业持续突破,中国制造的明天必将闪耀着智慧的光芒。
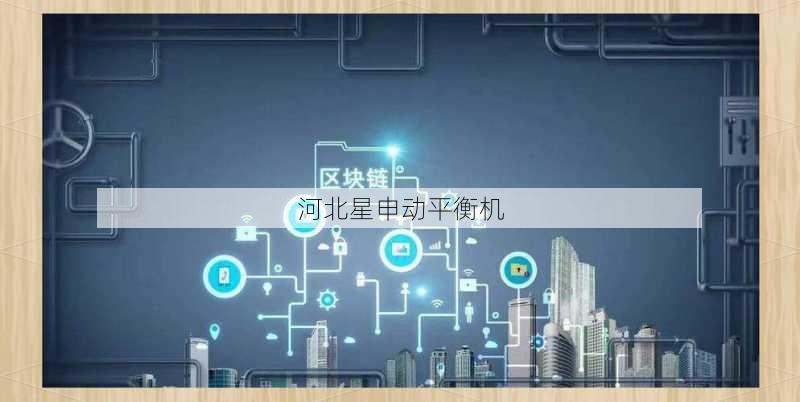