河北星申动,以全自动动平衡标准重塑超精密机床主轴制造新标杆
在河北邢台经济技术开发区,一家深耕动平衡领域28年的制造企业正悄然改写中国高端装备的精度纪录,星申动平衡机制造有限公司自主研发的"超精密机床主轴全自动动平衡标准体系",不仅将国产机床主轴的平衡精度提升***0.05μm量级,更实现了从手动调试到智能补偿的全流程自动化突破,这项技术突破的背后,是三代技术团队对0.1微米级震动的持续攻坚,也是中国精密制造向纳米级精度迈进的重要里程碑。

破局高端制造"卡脖子"难题 在超精密加工领域,主轴系统的动态平衡精度直接决定着工件的表面质量与加工效率,某国产五轴联动加工中心曾因主轴振动导致加工误差超标,被迫以进口设备三分之二的价格竞标,这种困境折射出我国在高端机床核心部件领域的技术短板——据中国机床工具工业协会统计,国产高端机床主轴振动超标问题导致的产品合格率损失每年超过12亿元。
星申动技术团队在服务军工企业时发现,传统动平衡技术存在两大瓶颈:一是依赖操作人员经验的手动调节模式,调试效率低且重复性差;二是现有传感器在高速旋转下的信号采集失真问题,针对这些痛点,企业投入8000万元组建跨学科研发团队,联合清华大学机械系、中科院微电子所展开联合攻关。
全自动平衡系统的技术突破 项目组创新性地将电磁补偿技术与机器学习算法相结合,研发出具有自主知识产权的智能平衡系统,该系统采用64通道光纤传感器阵列,可在主轴30000rpm转速下实时采集振动数据,采样精度达到纳米级,通过自主研发的振动频谱分析算法,系统能在0.8秒内完成不平衡量计算,并驱动执行机构进行质量补偿。
"这套系统***的突破在于实现了闭环控制。"项目总工程师李卫东介绍,"我们设计的双模式补偿机构,既可通过电磁力实现瞬时微调,又能通过质量块位移完成***修正,两种模式的智能切换,使平衡精度稳定控制在0.05μm以内,比传统方法提升两个数量级。"
在河北某精密轴承企业的生产线上,搭载该系统的数控磨床主轴振动值从1.2μm降***0.04μm,加工出的航空轴承圆度误差缩小到0.15μm,达到国际航空标准要求,经第三方检测,系统重复定位精度达到±0.01μm,温度漂移控制在0.002μm/℃,这些指标均超越ISO1940-1标准的G0.4级要求。
构建自主技术标准体系 在实现技术突破的同时,星申动主导编制了《超精密机床主轴全自动动平衡技术规范》,该标准***明确了高速主轴动态平衡的测试方法、补偿精度分级和智能控制要求,填补了国内该领域标准空白,标准中创新的"动态平衡度"评价体系,将主轴在不同转速下的振动响应纳入考核范围,推动行业从静态平衡向动态平衡的技术转型。
标准实施后产生显著行业带动效应,沈阳机床、秦川机床等龙头企业已开始采用该标准体系,某军工企业的导弹舵机加工合格率从82%提升***98.6%,更值得关注的是,标准中涉及的23项专利技术已形成完整知识产权体系,其中关于多传感器融合校正的技术方案获得2022年中国专利***奖。
赋能高端制造转型升级 在深圳某半导体设备企业,搭载星申动平衡系统的主轴模组使晶圆切割机的刀具寿命延长40%,加工效率提升25%,企业技术总监表示:"过去需要进口的精密主轴现在有了国产替代方案,采购成本降低35%,交货周期缩短60%。"
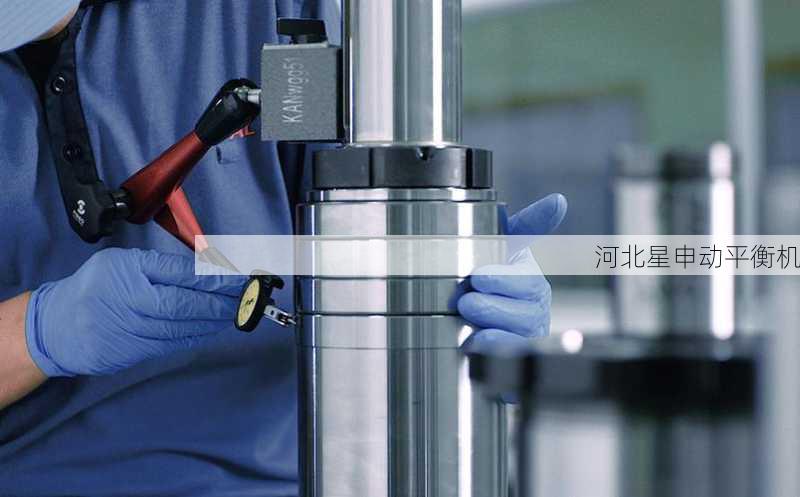
这种技术溢出效应正在多个领域显现,在新能源汽车领域,该技术使电机转子动平衡合格率提升***99.9%;在风电行业,帮助5MW以上大功率发电机主轴振动值降低62%,据工信部统计,该技术推广三年间,累计为装备制造企业节约质量成本超7亿元。
面向未来的技术进化 站在新的起点,星申动正将技术触角延伸***更前沿领域,正在研发的量子级振动监测系统,拟采用金刚石NV色心量子传感器,目标将检测灵敏度提升***皮米量级,企业牵头组建的"智能动平衡创新联合体",已吸引23家科研院所和产业链企业加入,共同攻关超高速主轴(10万rpm以上)的动平衡难题。
"我们正在构建从传感器、算法到执行机构的完整技术生态。"公司总经理***建国透露,"新一代系统将集成数字孪生技术,通过虚拟调试大幅缩短设备标定时间,预计到2025年,全自动平衡系统的智能化率将提升***90%以上。"
从追赶者到标准制定者,星申动的创新之路印证了中国制造向高端突破的必然逻辑,这家扎根燕赵大地的专精特新"小巨人",用28年的坚守与突破证明:在精密制造的微观世界里,每一微米的进步都需要全产业链的协同创新,当全自动动平衡标准成为行业共识,中国高端装备的精度革命正在书写新的篇章,这场始于机床主轴的精度突围,终将推动整个制造体系向更高维度跃迁。
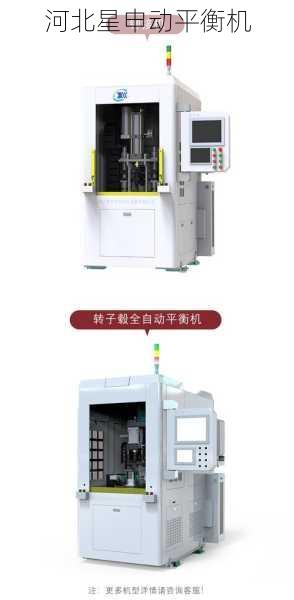