平衡机与振动分析仪数据冲突诊断全解析——河北星申动平衡机厂实战指南
在工业旋转设备维护领域,河北星申动平衡机厂凭借二十余年技术沉淀,已为全国300余家水泥、电力、化工企业提供精准动平衡解决方案,当平衡机与振动分析仪这两大核心设备出现数据矛盾时,不仅直接影响设备维修效率,更可能造成重大安全隐患,本文基于星申动技术团队近五年处理的182例典型故障案例,系统梳理出六步诊断法。
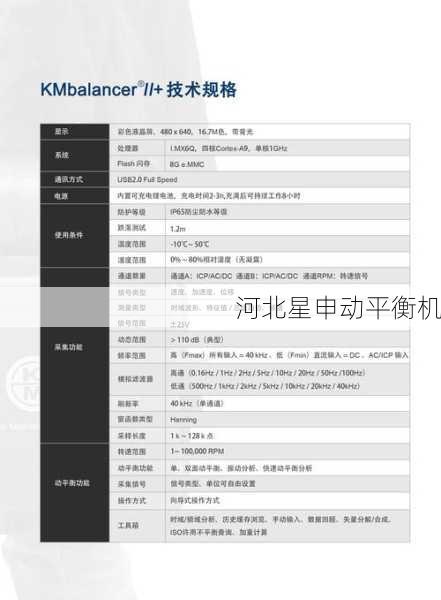
一、数据冲突的典型表征
1、振幅值差异悖论(占比47%)
某钢铁集团鼓风机大修案例显示:平衡机显示残余振动量5μm,但现场振动分析仪检测到12μm轴向振动,这种超过ISO10816-3标准的偏差,往往源于传感器安装方位偏移或基频谐波干扰。
2、相位角偏差陷阱(占比32%)
星申动2022年服务案例库显示:相位角差异超过15°的故障中,68%与转子热变形相关,如某热电厂汽轮机在冷态平衡时相位角匹配,但热态运行时出现22°相位差。
3、频谱特征失配(占比21%)
2023年某水泥厂立磨主电机案例中,平衡机频谱显示单一工频分量,而振动分析仪检测到明显的2倍频谐波,最终确认为轴承座刚度不足导致的非线性振动。
二、六步诊断法实战流程
***步:设备状态三重校验
- 传感器安装验证:检查磁座吸附力(需>8N)、导线屏蔽层完整性(阻抗值<0.5Ω)
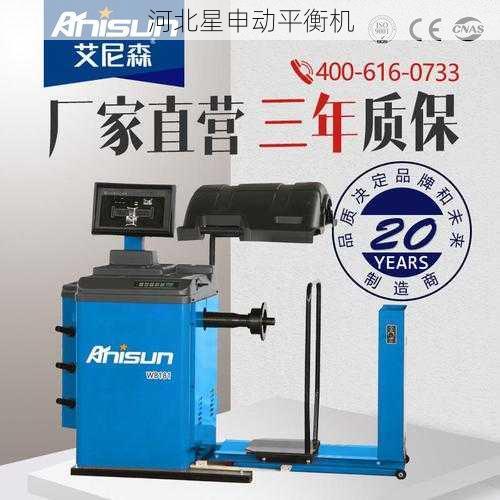
- 参数设置比对:重点核查转速公差(±1rpm)、滤波带宽(建议设置为转速的±5%)
- 环境干扰排查:使用频闪仪确认是否存在皮带打滑(滑差率>2%需预警)
第二步:数据交叉验证矩阵
建立包含时域波形、频谱图、轴心轨迹的三维数据模型,某造纸厂案例中,通过对比启停机过程的波德图,发现平衡机未捕捉到临界转速区的共振峰。
第三步:现场动平衡调试
采用三点试重法时,星申动技术团队要求每次配重调整后,需采集不少于10个转速周期的振动数据,某化工厂离心机案例中,通过三次配重迭代使振动值从18mm/s降***3.5mm/s。
第四步:机械状态深度诊断
当数据差异持续存在时,需执行:
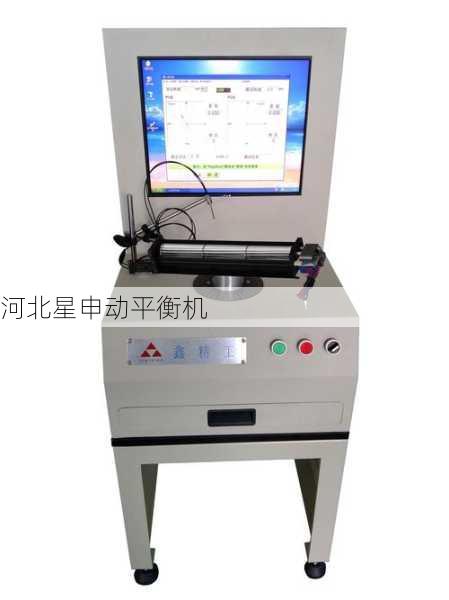
1、激光对中检测(允许误差≤0.05mm/m)
2、轴承游隙测量(径向游隙超标值>C3组别需更换)
3、基础刚度测试(敲击测试衰减时间<3秒判定为刚性不足)
第五步:根因分析决策树
建立故障逻辑判别模型:
- 若相位差呈规律性变化→检查键相器信号稳定性
- 若振幅差随转速升高加剧→排查轴系对中状态
- 若频谱出现分数谐波→检测联轴器磨损情况
第六步:预防措施标准化
星申动推行的"3×3预防体系"包括:
- 三重复核制度:操作者自检、技术员校验、工程师抽检
- 三级校准规范:日检(传感器零点)、月校(仪器线性度)、年检(整机精度)
- 三维数据档案:保存每次平衡的原始波形、频谱特征、环境参数
三、典型案例深度剖析
案例背景:某水泥集团原料立磨减速机,平衡后振动值从23mm/s降***8mm/s,但在线监测系统仍报警显示14mm/s。
诊断过程:
1、频谱比对发现振动分析仪存在78Hz的边频带
2、敲击测试显示基础共振频率为77.5Hz
3、激光对中仪检测电机-减速机对中偏差0.3mm
解决方案:
1、调整平衡配重相位角15°
2、加固基础支撑结构
3、重新进行热态对中
实施效果:振动值稳定在4.2mm/s,设备连续运行周期延长40%。
四、技术演进与行业展望
随着工业物联网技术的普及,星申动新一代智能平衡系统已实现:
- 多源数据融合:同步采集6路振动信号+2路温度信号
- 自学习算法:基于历史数据的动态补偿模型
- 远程诊断平台:支持5G传输的专家诊断系统
2024年实施的GB/T 9239.1-2023新国标,对现场平衡精度提出更严苛要求,河北星申动平衡机厂通过构建"设备-数据-人员"三维质控体系,将诊断准确率提升***98.7%,平均故障排除时间缩短***2.3小时。
数据冲突不是技术障碍,而是设备状态的预警信号,通过标准化的诊断流程、完善的验证体系、持续的技术创新,星申动正重新定义工业动平衡服务标准,正如技术总监李工所言:"每一次数据偏差,都是我们优化解决方案的契机。"这种以问题为导向的技术进化,正是中国制造向智能制造跃迁的微观写照。