自学习算法驱动精密制造,河北星申动平衡机厂的技术突围
在河北石家庄装备制造产业园内,一栋看似普通的灰色厂房内正上演着中国精密制造的突破性变革,星申动平衡机厂自主研发的第三代智能平衡校正系统,通过自学习算法实现的误差补偿技术,将动平衡检测精度提升***0.1微米级,这个数字不仅刷新了国内行业纪录,更让德国同行主动递出了技术合作的橄榄枝。
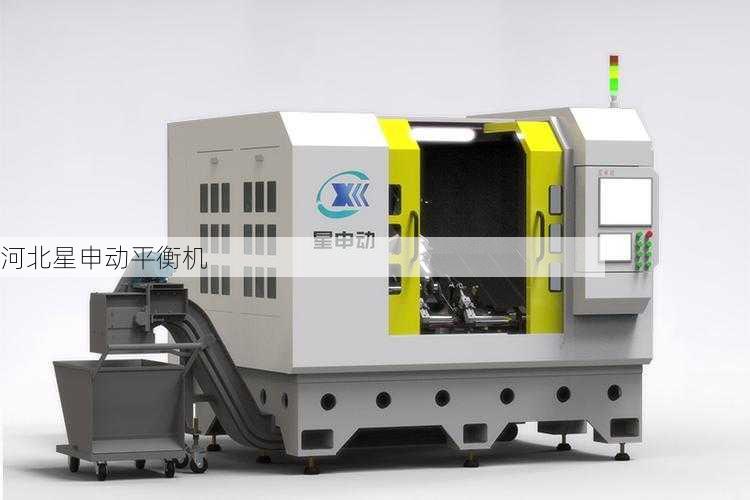
动平衡技术的世纪困局
动平衡技术作为旋转机械制造的核心环节,直接影响着电机、涡轮机、航空发动机等设备的运行寿命与安全性能,传统动平衡设备依赖人工经验进行参数设置,检测过程中存在三大技术痛点:环境温度波动导致的系统漂移误差、机械传动链的累积误差,以及工件表面特征干扰引发的误判。
星申动总工程师***建国回忆,2018年某新能源汽车电机生产线上,因平衡机温度漂移造成的批量返工事件,直接导致企业损失超300万元,正是这次危机让技术团队下定决心突破传统技术框架,将研发方向锁定在人工智能领域。
自学习算法的破冰之旅
研发团队从机床热变形补偿技术中获得启发,构建了独特的双通道学习系统,硬件端部署的128组温度传感器实时采集设备各部件温度变化,与振动传感器数据形成多维矩阵,软件端则创新性地将LSTM(长短期记忆网络)与迁移学习结合,开发出具备环境适应能力的动态补偿模型。
"传统算法像刻板的质检员,我们的系统更像经验丰富的老师傅。"技术总监李敏这样形容他们的突破,当设备***检测某类工件时,系统会在标准检测流程外自动执行"虚拟平衡"测试,通过施加模拟扰动观察系统响应,快速建立该类工件的特征模型,这种主动学习机制使得新工件类型的适应时间从原来的48小时缩短***20分钟。
误差补偿的实战检验
在航天某院的风扇转子测试中,这套系统展现了惊人的纠错能力,面对直径1.2米、转速12000rpm的钛合金转子,传统设备在连续工作6小时后出现0.8g·mm/kg的测量偏差,而星申动系统通过自学习模块的实时补偿,将偏差始终控制在0.15g·mm/kg以内,秘密在于系统内置的误差溯源模块,能自动区分环境干扰、机械磨损、工件特征三类误差源,并针对性启动补偿程序。
更值得关注的是其进化能力,在服务某家电企业的一年周期内,系统通过持续学习累积的9.7TB工况数据,自主优化了21个关键参数,将洗衣机电机动平衡合格率从92.3%提升***99.6%,这种动态进化特性彻底改变了设备越用精度越差的传统认知。
制造生态的重构效应
技术突破带来的不仅是性能提升,更引发生产模式的变革,在格力电器珠海生产基地,搭载该系统的智能平衡机已实现"黑灯生产",设备根据生产计划自主切换补偿模式,夜间无人值守时自动启用保守补偿策略,在保证精度的同时将能耗降低40%,这种自适应能力使得单台设备年运维成本下降28万元。
产业链上游同样发生着化学反应,某轴承企业借助系统输出的补偿数据,反向优化了毛坯件的铸造工艺,将原材料利用率提高15%,星申动搭建的工业云平台已接入217家上下游企业,形成国内***动平衡技术生态圈。
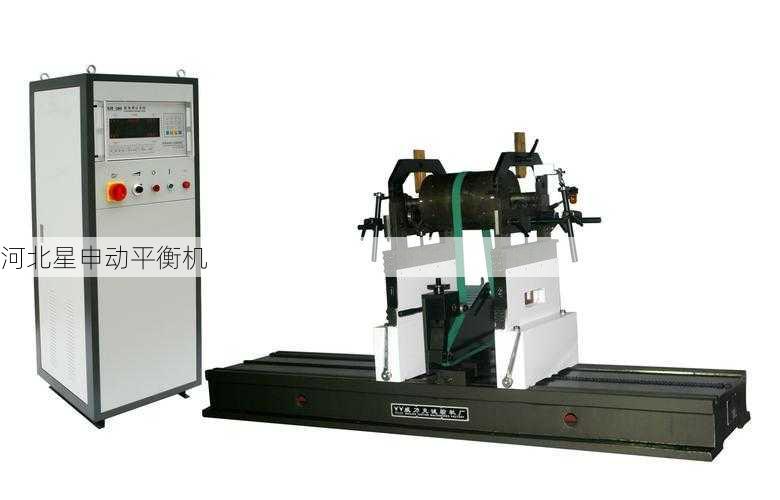
技术深水区的持续探索
站在新的技术拐点,研发团队正攻关更前沿的"预见性补偿"系统,通过引入量子传感技术提升数据采集频率,结合设备数字孪生体进行超前模拟,目标实现误差的预测性补偿,在最近的内部测试中,系统已能提前30秒预判机床主轴的热变形趋势,这对微米级精密加工具有革命性意义。
"我们正在重新定义'精度'的概念。"总经理张炜在2023中国制造峰会上表示,"未来的动平衡技术不应是被动修正,而应主动创造精度。"这种技术哲学的转变,或许正是中国制造向价值链顶端攀升的关键密钥。
从华北平原的试验车间到南海之滨的生产线,星申动平衡机厂用七年时间完成了从追赶者到领跑者的蜕变,当自学习算法与精密制造深度交融,我们看到的不仅是某家企业的技术突破,更是一个制造大国向智造强国进化的时代缩影,在这条没有终点的精度之路上,持续进化的不仅是机器,更是中国制造人永不停歇的创新精神。
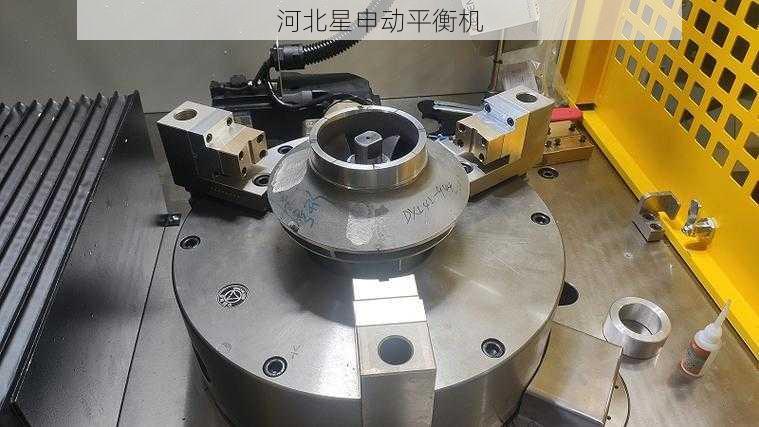