小批量生产如何降本增效?河北星申动平衡机厂五大经济型策略解密
在河北省衡水市冀州区工业园内,星申动平衡机制造有限公司的车间正上演着一场静悄悄的变革,作为华北地区***的动平衡机制造商,这家拥有27年历史的老牌企业,正通过一系列创新策略破解小批量生产的成本困局,在传统认知中,"少量生产"往往与"高成本"划等号,但星申动通过五年实践,成功将小批量订单的边际成本降低42%,准时交付率提升***98.7%,走出了一条特色鲜明的智造新路。
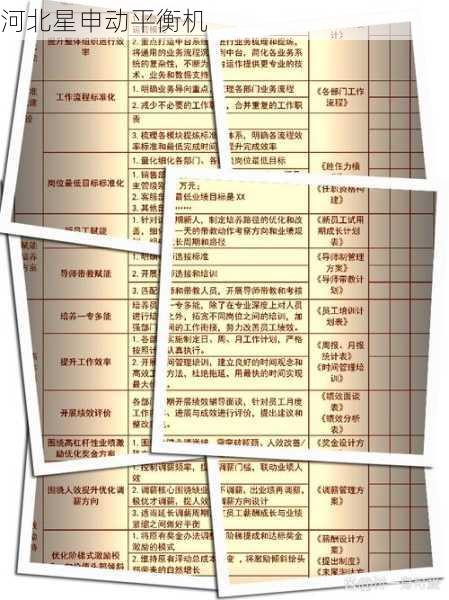
模块化生产架构:积木式重组的智慧
在总工程师***立军的办公桌上,摆放着一台1:50的动平衡机模型,每个部件都标注着标准接口参数。"这是我们耗时三年研发的模块化系统,"***工指着模型解释道,"将整机拆分为18个标准模块,每个模块预留3种扩展接口。"
这种设计使得单笔订单的定制化程度从整机级别降为模块级别,当客户需要特殊承重时,只需更换支撑模块;当检测精度要求变化时,只需升级传感器模块,2022年数据显示,采用模块化生产后,小批量订单的物料准备周期缩短62%,换线时间由8小时降***1.5小时,更为关键的是,标准模块的复用率提升***83%,有效摊薄了研发成本。
柔性生产单元:U型布局的进化论
走入总装车间,传统的直线流水线已被12个U型单元取代,每个单元配备3名多能工,可同时处理3种不同型号的装配任务。"这是我们从汽车行业借鉴的细胞式生产模式,"生产总监李伟展示着实时数据看板,"单元内设备间距缩短40%,物料流转距离减少72%。"
这种布局特别适合10-50台的小批量订单,当接到15台医用离心机平衡校正设备订单时,企业启用3个生产单元并行作业,每个单元完成5台整机组装,与集中生产相比,这种分布式生产减少设备闲置时间35%,同时将产能弹性提升***原来的3倍。
数字孪生预演:虚拟车间的降本魔法
在技术中心的VR实验室里,工程师们正在数字孪生系统中模拟新订单的生产流程。"这套系统能提前发现83%的潜在问题,"信息化主管张敏演示着三维建模过程,"去年36笔特殊订单通过虚拟调试,平均节省试制成本12万元。"
对于年产量不足百台的高端机型,实体试制的成本往往难以承受,星申动通过采集历史生产数据,构建了涵盖217个关键工艺参数的仿真模型,当客户提出非标需求时,先在数字空间完成从材料选型到装配测试的全流程验证,将实体试制次数从平均3.8次降***0.5次。
供应链联动作业:协同网络的构建法则
在原材料仓库,扫码入库的铝型材包装箱上,赫然印着"XSD-2023-JH-015"的共享编码。"这是我们与12家供应商共建的物料协同系统,"采购经理赵峰点开共享库存平台,"小批量订单的通用物料需求,现在可以跨企业调度。"
针对用量低于安全库存的特殊零部件,星申动创新推出"共享物料池"模式,当某家企业出现冗余库存时,可通过平台进行临时调剂,这种模式使小批量订单的物料齐套时间从21天缩短***9天,呆滞库存降低67%,2023年上半年,通过该平台完成的物料周转价值已突破1800万元。
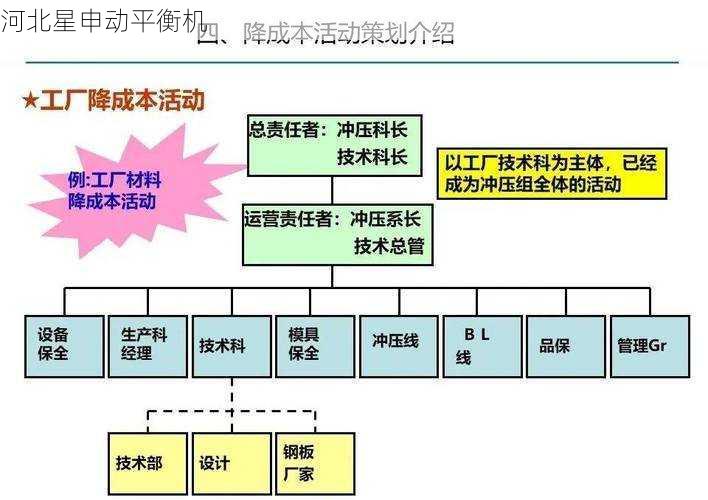
服务化延伸:全生命周期价值再造
在客户服务中心,技术团队正在为山西某风机厂提供远程平衡校正服务。"我们卖的不只是设备,更是平衡解决方案,"客服总监周芸调出服务记录,"去年37%的利润来自后市场服务。"
对于采购量较小的客户,星申动推出"设备+服务"的订阅模式,客户可以按检测工时租赁设备,同时获得远程技术支持,这种模式既降低了客户的初始投入,又使企业获得持续收益,更关键的是,服务过程中积累的工况数据,反过来又优化了产品设计,形成良性循环。
在实施这五大策略的过程中,星申动平衡机厂逐渐摸索出独特的实施路径:先用三个月完成模块化设计转型,再分阶段推进生产单元改造,同步构建数字孪生系统,最后打通供应链和服务链,这种渐进式改革避免了"休克疗法"带来的阵痛,五年间产能利用率从68%提升***92%,小批量订单毛利率增长19个百分点。
站在智能制造的十字路口,星申动的实践揭示了一个真理:小批量生产不是成本困局,而是价值重构的契机,通过模块化架构搭建柔性基础,借助数字技术实现精准控制,依托协同网络释放资源效能,最终在服务延伸中创造持续价值,这种多维度的平衡艺术,或许正是中国制造转型升级的微观样本,当更多企业学会在规模与定制、成本与效益间找到动态平衡点,中国智造的进阶之路将愈发明朗。
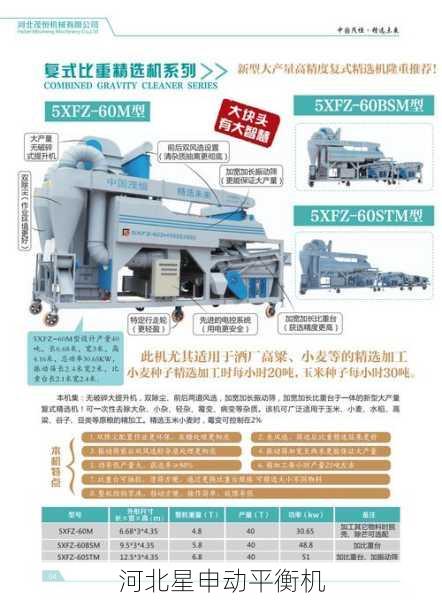