构建专业化培训体系 夯实制造业人才根基——河北星申动平衡机厂***职业技能标准落地实践
制造业转型背景下的技能人才需求
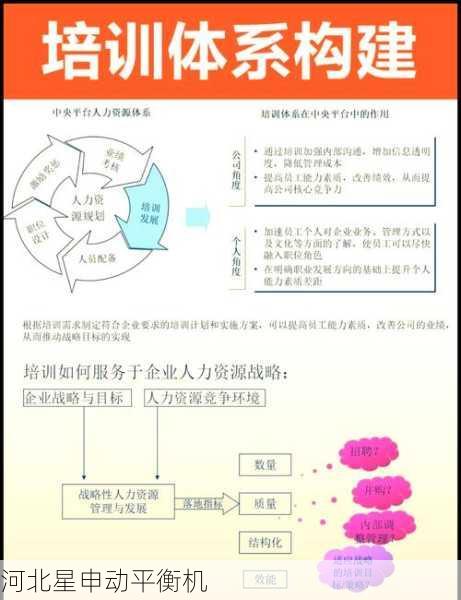
在"中国制造2025"战略深入推进的当下,河北星申动平衡机厂作为华北地区重要的精密机械制造企业,正面临产业升级与人才需求的结构性矛盾,企业自主研发的第三代动平衡检测设备已实现0.001mm的测量精度,但设备操作人员的技能水平却成为制约产能释放的关键瓶颈,据2023年企业生产数据显示,因操作不当导致的设备停机时间占总工时的17.3%,直接经济损失达年度产值的2.8%,这一现实矛盾推动企业将目光聚焦于操作员培训体系的系统性重构,通过深度对接***职业技能标准,探索出了一条独具特色的技能人才培养路径。
一、***职业技能标准的体系化解析
《***职业技能标准——平衡机操作员(2022版)》将职业能力划分为设备操作、工艺实施、质量控制三个核心维度,构建了"5级15阶"的能力评价体系,星申动技术团队通过为期半年的标准解读,提炼出三个关键着力点:
1、标准化作业流程(SOP)建设
对标标准中"设备调试误差≤0.05mm"的技术要求,将原有23项操作规程细化为56个标准动作单元,例如在动平衡检测环节,将传统的"三点定位法"升级为"五步校准流程",通过增加激光辅助定位和温度补偿步骤,使校准效率提升40%。
2、动态知识图谱构建
依据标准中的知识权重分配表(基础理论30%、设备操作45%、故障诊断25%),开发出模块化培训课程,特别强化了"设备振动频谱分析"等核心模块,将理论培训时长从48学时增***72学时,并引入AR模拟训练系统。
3、多维度评价体系创新

在***标准要求的理论+实操考核基础上,增加"异常工况处置能力"评估项,开发包含27类典型故障的仿真测试系统,要求学员在15分钟内完成故障诊断与处置方案制定。
二、企业培训体系的创新实践
星申动平衡机厂建立的"三维立体"培训体系,实现了***标准与企业实践的有机融合:
1. 师资队伍建设
组建由8名***技师、2名设备工程师、1名质量管控专家构成的培训团队,其中***培训师李建国参照***职业技能鉴定标准,开发出"四段式"教学法:
- 基础认知阶段:利用3D建模技术分解设备内部构造
- 模拟操作阶段:在数字孪生系统中进行无风险训练
- 实战演练阶段:在隔离生产区进行真实工况操作
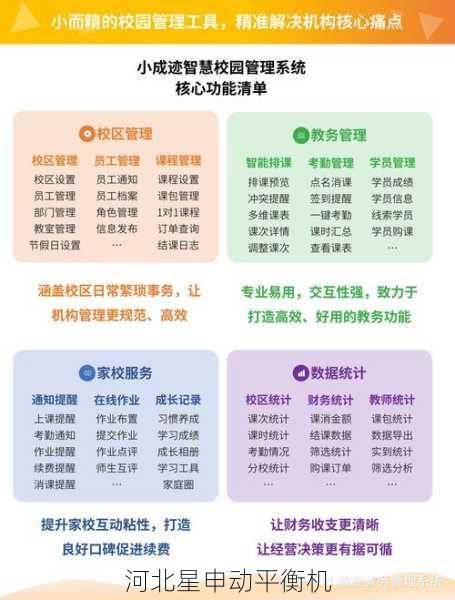
- 能力拓展阶段:参与设备改良项目的可行性论证
2. 培训设施升级
投资380万元建成华北***动平衡实训中心,配置:
- 全系列设备操作工位(包含5代机型)
- 智能考核系统(自动记录操作轨迹并生成评估报告)
- 远程诊断终端(直连德国申克技术服务中心)
- 数据可视化墙(实时显示200+设备运行参数)
3. 培训-生产联动机制
建立"培训学分银行"制度,将培训成果与岗位晋升直接挂钩:
- 初级操作员需累计120学分(含80学分的设备维保专项)
- 中级操作员须主导完成3项工艺改进项目
- ***操作员需通过德国TÜV认证考核
三、标准落地的具体成效
经过两年实践,培训体系显现出显著成效:
1、技能水平提升
2023年职业技能鉴定通过率达92.7%,较体系实施前提升41个百分点,***工占比从12%增***35%,培养出2名省级技术能手。
2、生产效率改善
设备平均故障间隔时间(MTBF)延长***1800小时,产品一次交验合格率提升***99.3%,某新能源汽车电机转子的动平衡校正时间从25分钟缩短***16分钟。
3、技术攻关突破
受训人员参与的"高速转子在线检测系统"研发项目,成功将检测精度提升***ISO1940 G1.0级,获得3项实用新型专利。
四、典型案例分析
2023年承接某航天部件制造企业的紧急订单时,操作员***伟运用培训中所学的"振动相位分析法",在设备报警阈值未触发前,通过细微的频谱异常判断出主轴轴承预紧力失衡,避免了一起可能造成百万元损失的质量事故,这个案例被编入企业《典型故障处置手册》,并作为***标准应用示范案例上报工信部门。
五、行业示范效应与未来展望
星申动的实践已产生显著行业影响:
- 牵头制定《动平衡设备操作规范》团体标准
- 成为3所职业院校的定点实训基地
- 为12家上下游企业提供培训方案输出
面对智能制造发展趋势,企业正在推进:
1、开发基于数字孪生的智能培训系统
2、建立跨企业技能认证联盟
3、探索"新型学徒制"校企合作模式
标准***下的制造业人才培育新范式
河北星申动平衡机厂的实践表明,***职业技能标准不是僵化的条文框架,而是可以与企业实际深度结合的创新指南,当标准的普适性要求与企业的个性化需求产生化学反应时,就能培育出既符合行业规范又具备企业特质的技能人才队伍,这种"标准为基、企业为体、创新为魂"的培训体系,正在为制造业高质量发展构筑起坚实的人才基石。