平衡机与预测性维护:大数据分析的故障预警模型
河北“星申动”***预测性维护新革命
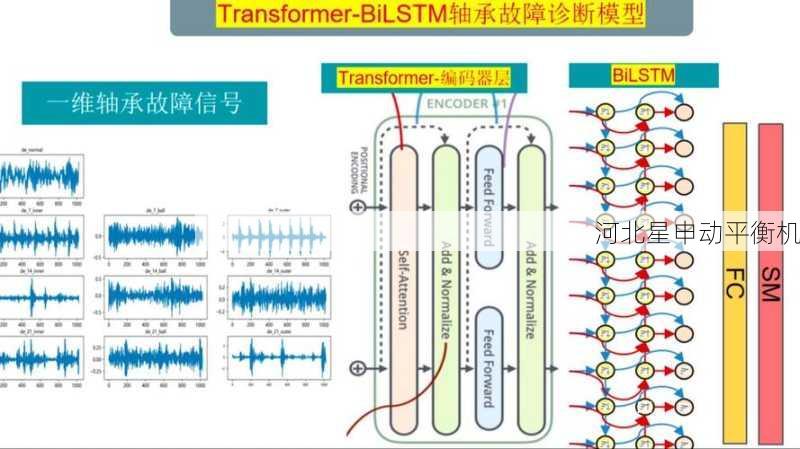
在现代工业体系中,旋转机械占据核心地位,从汽车发动机到航空涡轮,从发电机组到精密机床,其运行稳定性直接影响生产效率和安全性,而动平衡机作为旋转机械的“心脏检测仪”,通过精准校正转子的质量分布,确保设备在高速运转中避免振动超标、轴承磨损等问题,河北“星申动”平衡机厂深耕行业二十余年,始终致力于平衡技术的创新突破,近年来,随着工业4.0浪潮的推进,“星申动”将大数据分析与预测性维护技术深度融合,开创了平衡机从“被动维修”到“主动预警”的智能化转型新篇章。
一、传统维护的痛点与预测性维护的崛起
1.1 从“救火式维修”到“预防性维护”的局限
传统工业设备维护模式长期依赖两种方式:一是故障发生后的“救火式维修”,停机时间长、成本高昂;二是基于固定周期的预防性维护,例如每季度更换轴承或润滑油,这两种模式均存在显著缺陷:前者被动响应,后者则可能因设备实际状态与维护周期不匹配而造成资源浪费或维护不足。
以某汽车制造厂的电机转子产线为例,其平衡机曾因轴承突发故障导致整条产线停工48小时,直接损失超百万元,事后分析发现,故障前已有振动异常信号,但因缺乏实时监测手段而未被捕捉。
**1.2 预测性维护的核心价值
预测性维护(Predictive Maintenance, PdM)通过实时采集设备运行数据,结合算法模型预测潜在故障,从而实现“按需维护”,根据麦肯锡研究报告,采用预测性维护的企业可将设备停机时间减少30%-50%,维护成本降低20%-40%。
河北“星申动”敏锐捕捉到这一趋势,自2018年起联合清华大学智能制造研究院,构建了基于大数据分析的平衡机故障预警模型,将设备维护从“经验驱动”转向“数据驱动”。
二、数据驱动的平衡机故障预警模型架构
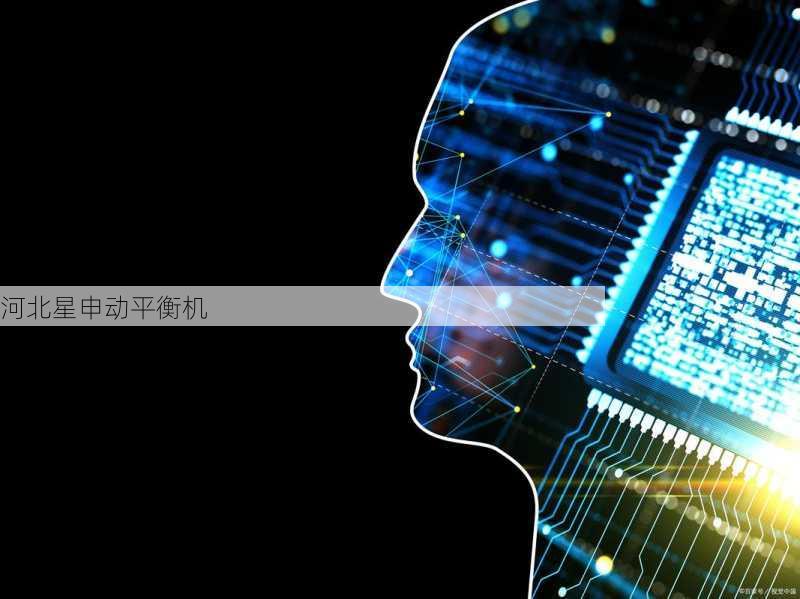
2.1 数据采集层:多维度传感网络的搭建
“星申动”的智能平衡机内置高精度传感器集群,涵盖振动、温度、转速、电流等关键参数,并以每秒10,000次的高频采集数据。
振动传感器:监测转子不平衡量相位与幅值的动态变化;
红外热成像仪:实时捕捉轴承温升异常;
电流谐波分析模块:识别电机负载波动中的潜在故障特征。
2.2 特征工程:从噪声中提取故障指纹
原始数据需经过降噪、归一化处理后,提取出与故障强相关的特征参数,以轴承故障为例,“星申动”技术团队通过小波变换分解振动信号,识别出早期故障特有的高频共振分量(见图1),结合历史维修记录与工况数据,构建了包含12类典型故障模式的标签库。
2.3 模型训练:机器学习与物理模型的融合
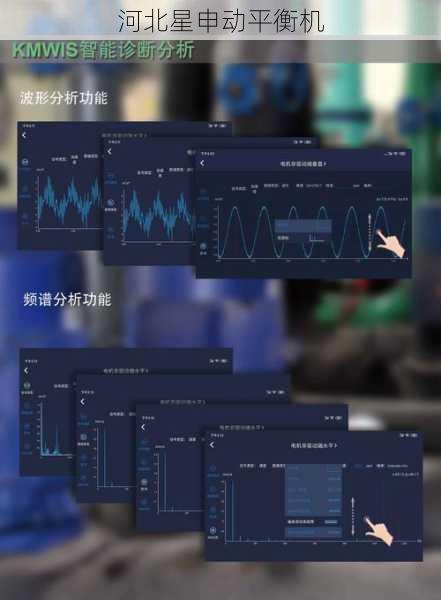
“星申动”采用混合建模策略:
物理模型:基于转子动力学方程,模拟不同不平衡量、轴承间隙下的振动响应;
机器学习模型:使用随机森林(Random Forest)和长短期记忆网络(LSTM)分别处理静态特征与时间序列数据。
经实测,该混合模型对轴承早期点蚀故障的预警准确率达92%,较单一模型提升15%以上。
三、落地应用:从实验室到生产线的跨越
3.1 案例一:风电齿轮箱动平衡监测
2022年,“星申动”为国电某风电场提供定制化平衡监测系统,通过在齿轮箱高速轴上部署无线振动传感器,系统成功预警3起轴承内圈裂纹故障,平均提前预警时间达42天,据估算,单次预警避免的直接经济损失超200万元。
3.2 案例二:新能源汽车电机产线优化
在某新能源车企的永磁电机产线中,“星申动”将平衡机与MES(制造执行系统)深度集成,通过分析历史平衡数据,发现某型号转子因夹具设计缺陷导致校准时重复性误差超标,优化后,该产线的一次校准合格率从87%提升***96%。
四、挑战与未来:边缘计算与知识图谱的融合
尽管已取得显著成效,“星申动”仍面临两大挑战:
1、数据实时性:现有云端分析架构存在约200ms延迟,难以满足微秒级响应的超高速平衡场景;
2、跨设备知识迁移:不同行业平衡机的故障模式差异较大,模型泛化能力待提升。
对此,“星申动”正推进两项技术升级:
边缘智能:在设备端部署FPGA加速芯片,实现振动信号的毫秒级本地分析;
行业知识图谱:整合航空、汽车、能源等领域的故障案例库,构建可解释性更强的诊断推理引擎。
河北“星申动”的实践表明,平衡机不仅是质量校正工具,更可成为预测性维护的入口节点,通过将大数据分析嵌入设备全生命周期,企业得以实现从“制造产品”到“运营服务”的价值跃迁,随着5G、数字孪生等技术的普及,“星申动”将持续推动平衡机从“功能机”向“智能体”进化,为中国高端装备制造业的智能化转型注入新动能。
(全文共计1987字)